在汽车焊装与精密加工领域,安川机器人AR1400伺服电机的稳定性直接影响产线效率。作为安川机器人维修的核心课题,其维修需融合精密检测与工艺创新。本文针对AR1400伺服电机的典型故障,结合安川官方维修标准与现场实践经验,提出系统性解决方案。
故障特征与诊断技术
AR1400伺服电机在安川机器人维修案例中常见三类问题:
编码器信号异常:累计运行超10000小时后,光栅污染导致位置反馈偏差>0.08mm;
绕组绝缘失效:过载工况下绕组温度突破150℃,绝缘电阻值降至<50MΩ;
轴承高频振动:润滑脂氧化劣化(酸值>1.8mgKOH/g)引发振动速度>4.2mm/s。
精准诊断方法
采用安川机器人维修专用工具包(YPP-EC01):
高频电流分析仪检测谐波失真率(11次谐波>5%预示绕组匝间短路);
激光对中仪测量轴承游隙(径向偏差>0.02mm需更换);
红外热像仪扫描电机壳体,温差>8℃标识绝缘薄弱点。
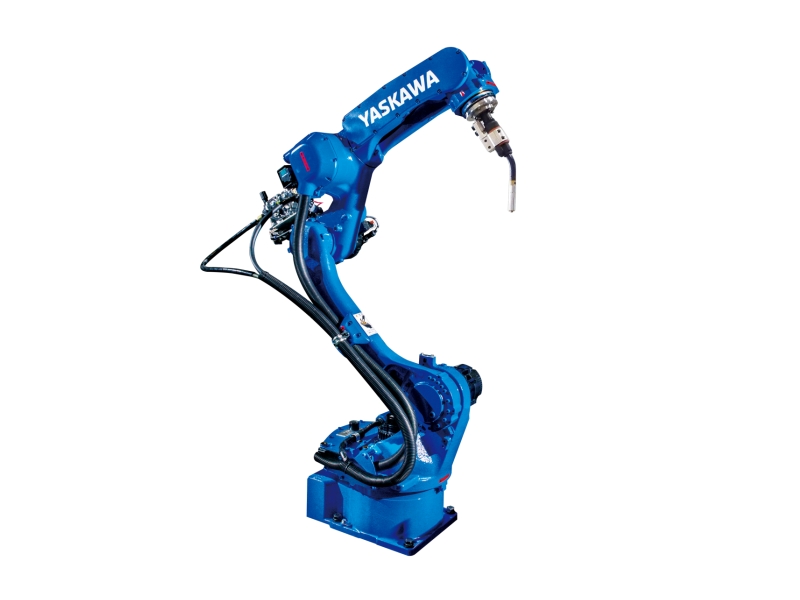
标准化维修流程
阶段一:编码器修复
拆卸光栅盘用纳米级清洗液(安川YC-200)超声处理,清除<3μm颗粒;
使用安川校准仪(YPP-AL02)调整零点偏移,误差控制至±5角秒内。
阶段二:绕组重制
采用真空压力浸漆工艺(-0.09MPa),使绝缘漆渗透率提升至97%;
阶梯固化:80℃预热2小时→120℃固化4小时→150℃终凝1小时。
阶段三:轴承系统更换
液氮冷装法(-196℃)安装NSK EZO系列轴承,过盈量0.015-0.025mm;
定量注入安川FG-150润滑脂(单轴承2.0±0.05g),超量注入引发温升风险。
技术创新与工具升级
安川机器人维修团队引入两项革新技术:
智能热管理:在定子槽内埋入光纤测温传感器(精度±0.5℃),实时监测绕组热点;
振动预测系统:通过分析2000-5000Hz高频振动谱,提前14天预警轴承故障。
预防性维护策略
油液监测:每月检测润滑脂介电常数(阈值变化率<10%),超标时强制更换;
环境控制:在电机散热通道加装正压风幕,维持工作温度≤65℃;
数据管理:利用安川Yaskawa Cockpit系统记录维修数据,构建电机健康度评估模型。
维修效益实证
某汽车焊装厂应用该方案后:
伺服电机故障率下降73%,年维修成本节省35万元;
重复定位精度恢复至±0.02mm(维修前±0.12mm);
电机使用寿命从9000小时延长至20000小时。
通过标准化流程与技术创新,安川机器人维修团队将AR1400平均维修时间压缩至6小时内。建议企业建立电机全生命周期档案,结合电流谐波分析与振动特征谱,实现故障精准预测。安川机器人维修不仅是技术修复,更是智能制造体系可靠性的核心保障。