传统焊接保护气供应多采用固定流量模式,难以契合复杂多变的焊接工况。安川焊接机器人在执行任务时,面对不同厚度、材质的焊件,以及多样的焊缝形状和焊接速度,固定流量供气在焊接需求较低时,造成大量保护气浪费,增加企业运营成本;在关键焊接环节,又因保护气供给不足,导致焊缝出现气孔、裂纹、未熔合等缺陷,严重影响焊接质量与产品可靠性。
安川焊接机器人节气装置专为解决这些痛点精心打造。其核心是一套智能调控系统,与安川焊接机器人深度融合,宛如装置的 “智慧大脑”。该系统通过一系列高精度传感器,实时监测焊接过程中的关键参数。电流传感器能精准捕捉焊接电流瞬间变化,焊接电流波动直接反映焊接区域热量产生及金属熔化状态,进而体现对保护气保护强度的需求;电压传感器敏锐监测电弧电压起伏,为判断焊接电弧稳定性提供关键数据,辅助调节保护气流量;速度传感器实时追踪焊接速度,以便根据不同速度下保护气覆盖需求差异进行动态调控;针对复杂焊缝,装置还配备先进的视觉传感器,精确识别焊缝形状、位置以及熔池动态变化,全方位收集焊接实时信息。
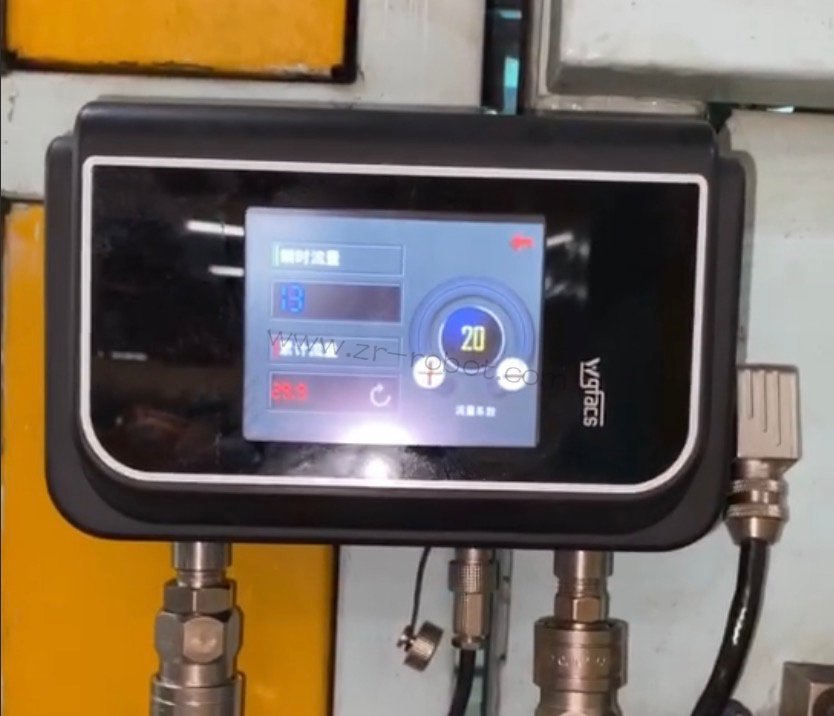
在某汽车零部件制造企业,安川焊接机器人焊接铝合金薄壁部件时,焊接速度快且电流变化频繁,节气装置迅速响应,自动增大保护气流量,确保焊接区域始终处于良好保护氛围,有效避免气孔、氧化等缺陷。焊接汽车底盘厚板部件时,焊接过程相对平稳,装置则适当降低保护气流量,避免浪费。
与传统供气方式相比,安川焊接机器人节气装置优势显著。节能方面,实际应用数据显示,使用该装置后,保护气消耗量可降低 30%-50%,为企业节省大量成本。提升焊接质量上,精准保护气供给营造稳定焊接环境,有效减少焊接缺陷。该汽车零部件制造企业引入安川焊接机器人节气装置后,产品一次合格率也大幅提高,同时每年节约保护气成本超百万元。
目前,YASKAWA焊接机器人节气装置已在汽车制造、机械加工、电子设备制造等多家企业成功应用。随着技术不断成熟完善,其必将在更多涉及焊接工艺的领域广泛推广,助力企业实现高效、节能、优质的绿色生产目标,推动焊接行业迈向智能化、节能化发展新阶段。